Retrofitted used machines
To do retrofit of an used CNC machine often makes more sense than buying the new one. The such machine can be up to 60% cheaper.
In addition, delivery times for an refurbished machine is shorter and the existing tools and clamping fixtures can be used.
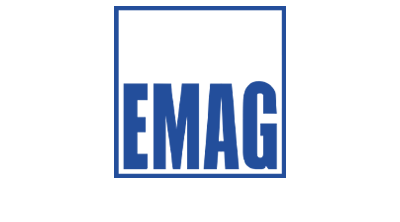
VL5
Year of manufacture: 2005.
Year of retrofit: 2022.
RETROFITTED MACHINE
SPECIAL OFFER
TECHNICAL DATA – EMAG VL5
WORKING AREA
Chuck diameter |
mm |
250 |
Swing diameter |
mm |
260 |
X – travel |
mm |
570 |
Z – travel |
mm |
200 |
MAIN SPINDLE
Spindle nose |
size |
6 |
Spindle bearing, front |
mm |
110 |
Spindle speed, max. |
min-1 |
4500 |
MAIN DRIVE
AC – asynchronous motor |
kW |
22 / 18 |
Max. load at |
min-1 |
850 |
Torque 40 / 100 % ED |
Nm |
250 / 202 |
FEED DRIVE
Rapid traverse speed in X |
m / min |
60 |
Rapid traverse speed in Z |
m / min |
30 |
Feed force in X / Z |
kN |
5 |
Ball sreew diameter X / Z |
mm |
40 / 40 |
DISC-TYPE TURRET
EMAG disc-type turret, |
||
VDI tool holder with diameter 40 mm, fast rotating of the disc-type turret with the cooling system |
||
All places have possibility for driven tool |
||
Standard and number of tool places |
DIN 69 880 |
12 places |
Tool holder diameter |
mm |
40 |
Max. speed of driven tool |
min -1 |
6. 000 |
Torque at 10% |
Nm / kW |
40 / 8,5 |
Torque at 40% |
Nm / kW |
24 / 7,5 |
Torque at 80% |
Nm / kW |
17 / 5,5 |
Torque at 100 % |
Nm / kW | 15 / 3,5 |
OPTION - TURNING AND MILLING
Interpolation with C, X and Z axis for slot milling, spline, etc. |
|
Milling speed |
from 0 to 100 min-1 |
Position precision of the spindle |
+ / – 0, 01 degrees |
Programming possibility |
0, 001 degrees |
CONVEYOR A – OS
The conveyor is and additional A-axis on the machine which is very easy to program it and adjust it to the diameter of the workpiece. The machine takes raw-parts at the PICK-UP station, spindle goes into working area, after machining is done, completed part is left again on the PICK-UP station and conveyur rotates. Transport of the pallets (prisms) with the workpieces are performed via chain.
The workpieces are easily picked up and left at the programmes position of the machine (asymmetrical pieces can also be machined)
Number of the pieces at the conveyour 30 |
diameter |
Number of the pieces at the conveyour 18 |
diameter |
Number of the pieces at the conveyour 14 |
diameter |
Max. workpiece height |
110 (145) mm |
Max. workpieces weight |
10 kg |
CHIP CONVEYOR
Chip conveyor is designed for dry and wet machining.
Disposal of the chips is at height of 1250 mm.
Emulsion tank capacity 300 l.
On the conveyor is installed the pump with next characteristics 80 l / min – 7 bar pressure.
ELECTRICAL EQUIPMENT
Operating voltage |
V |
400 |
Control voltage DC |
V | 24 |
Control voltage AC |
V |
230 |
Frequency |
Hz |
50 |
Total installed power rating |
kW |
40 / 42 |
Lead fuse |
A |
63 |
WEIGHTS AND DIMENSIONS
Lenght (with chip conveyor) |
mm |
2.700 (3.800) |
Widht |
mm | 3.800 |
Height |
mm |
2.100 |
Weight |
kg |
7.000 |
COLOR
The paint on the machine and chip conveyor is resistant to the emulsion
RAL 7035 i RAL 5023 ( base )
RETROFITTED ON THE MACHINE
MAIN SPINDLE
• All bearings are changed
• All sealings are changed
• The stator has bees inspected by an authorized service center
FEED DRIVE - X AXIS
• New X-axis ball screw and axial-radial bearing were installed
• New X-axis linear guides were installed
• New sprockets and belt were installed
• Linear glass scale was serviced by authorized Heidenheim service
• New metering devices were installed on the central lubrication system
• New hardware protections (bumpers) were installed
FEED DRIVE - Y AXIS
• New Z-axis ball screw and axial-radial bearing were installed
• New Z-axis linear guides were installed
• New brake is installed
• New sprockets and belt were installed
• Linear glass scale was serviced by authorized Heidenheim service
• New metering devices were installed on the central lubrication system
• New hardware protections (bumpers) were installed
DISC-TYPE TURRET
• New sealing elements are installed
• New bearings all installed
• New motor and gearbox of driven tools are installed
• New measurement system
WORKING AREA
• New safety glass was installed
• New wippers were insatlled
• New sealing elements were installed
• New lights weer installed
• New nozzles are installed
HYDRAULIC / PNEUMATICS
• Hydraulic accumulator was recharged
• New hoses were installed
• New hydraulic filter was installed
• New air preparation unit was installed
• New hydraulic valves are installed (system, clamping cylnder, disc turret)
ELECTRO
• New singal light is installed
• New sensor cables
• New temperature sensor
• New power supply module
• New regulator of driven tools motor
• New operating panel (On/Off, Not-Aus, key)
WORKPIECE CONVEYOR - A AXIS
• New bearings were installed
CHIP CONVEYOR
• New bearings were installed
• Emulsion pump was refurbished
• New emulsion filter housing with 2 cartidges were installed
COOLING UNIT / EXHAUST
• Cooling unit was refurbished
• Coolant fluid was replaced
• New exhaust filters were installed
COLOR
• Parts were sandblasted before painting
• The paint on the machine and chip conveyor is resistant to the emulsion
RAL 7035 i RAL 5023 ( base )
Videozapisi rada stroja
Pogledajte kako radi stroj EMAG VL5
Želite li saznati više?
Dozvolite da Vam predstavimo sve mogućnosti i posebnosti EMAG strojeva i pomognemo Vam odabrati najbolju opciju za Vaše potrebe!