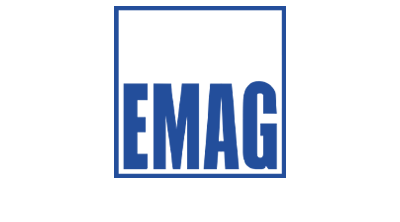
INDUCTION
HARDENING MACHINES
INDUCTION HARDENING
Induction hardening offers significant advantages over traditional methods for heat treatment of steels, alloys and other metal parts. This process is perfect for metals with a carbon content more than 0,3$, especially steels with a low content of alloying elements (C34, C35, C60, …). As descried in DIN EN 100083.
PROCESS
The process is very demanding for equipment and coil. Ideal curing results can only be achieved by perfectly matching a precisely controlled energy source with an optimal induction coil design. Experienced Eldec engineers adjust the induction coils to meet customer specifications. Each machine is fully inspected and tested to ensure optimal settings.
Induction hardening is a process in which heat is generated directly in a workpiece. The main advantage of this type of heat treatment is that the material quickly reaches the desired temperature to harden the metal parts. By traditional processes such as flame, furnace or convection, heat is brought to the workpiece by heating the surface layer. These methods take significantly more energy. In contrast, induction hardening offers an extremely short hearting time. In addition, the power, frequency and geometry of the inductor can be precisely controlled. This minimizes workpiece deformations and ensures greater process efficiency.
PRINCIPLE HOW IT WORKS
One or more induction coils are used to create and direct an alternating magnetic field. This magnetic field creates eddy currents in the metals, which heat the workpiece to the desired temperature. immediately after heating, the workpiece goes through a quenching process using water, oil or emulsion. With this, we achieve martensitic transformation. After quenching, the workpiece is subjected to tempering, in order to achieve the desired ratio of hardness and toughness. The curing depth is controlled, very precisely, by adjusting the power source and the frequency of the induction coil current. The thickness of the heated layer from the surface of the metal to some point below the surface is inversely proportional to the frequency of the applied alternating current. Higher frequencies produce a thinner layer.
MIND-L 1000
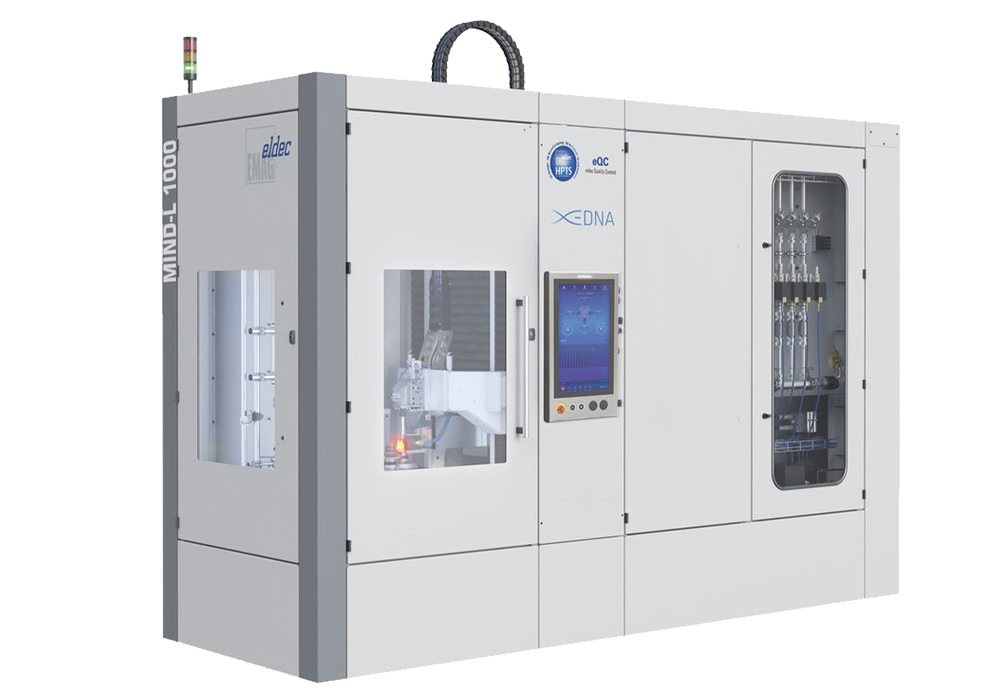
Advantages
|
Modular and compact design allow for custom hardening solution |
Simultaneous hardening, annealing and additional functions owing to vertical rotary table concept |
|
10 – 1,000 kW energy sources |
|
Integrated slim gantry automation (optional) |
|
Easy integration into EMAG line system |
|
Workpiece lenght, max. |
800 mm |
Workpiece diameter, max. |
160 / 200 mm |
Workpiece weight, max. |
10 kg |
Generators |
10 / 1.000 kW |
Want to know more?
Let us present you all the possibilities and special features of EMAG machines and help you choose the best option for your needs!